Membrane filters, a crucial component in numerous industrial processes, play a pivotal role in achieving selective separation, purification, and concentration of substances. These filters are designed to allow specific components to pass through while retaining or removing undesired particles, molecules, or contaminants. Their application spans diverse industries, ranging from water treatment and pharmaceuticals to food and beverage production, with each industry benefiting from tailored membrane filtration techniques to address specific needs.
At its core, the primary function of membrane filters is to facilitate a separation process based on size, charge, or other molecular properties. These filters are constructed using porous materials that create a barrier, allowing the passage of molecules of a certain size or characteristics, while preventing larger or undesirable components from passing through. The effectiveness of membrane filtration lies in its ability to achieve separation without relying on harsh chemicals or excessive energy consumption, making it an environmentally friendly and efficient option for various industrial applications.
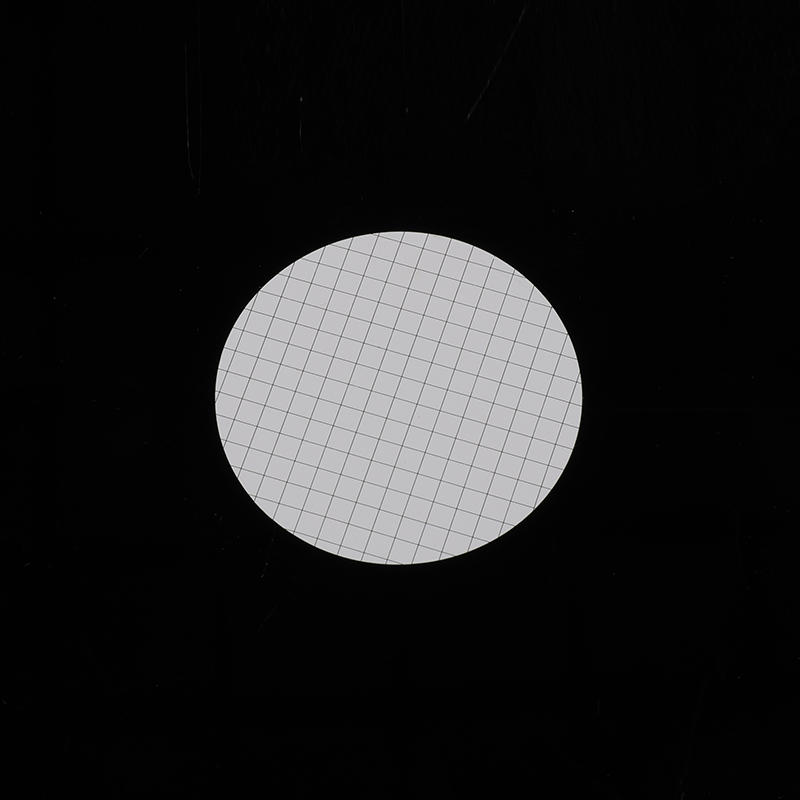
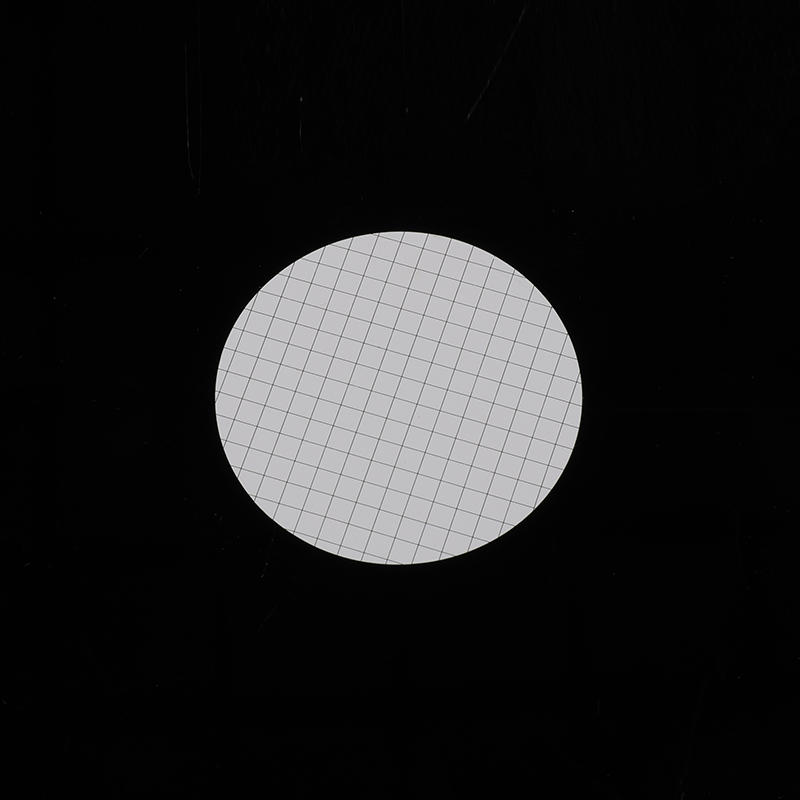
One of the most common uses of membrane filters is in water treatment. Here, membranes aid in the removal of suspended solids, bacteria, viruses, and other contaminants from both potable and wastewater sources. The different types of membrane filters, such as microfiltration, ultrafiltration, nanofiltration, and reverse osmosis, allow for varying degrees of particle size exclusion. Microfiltration membranes, for instance, are adept at eliminating larger particles, while ultrafiltration and nanofiltration membranes target smaller contaminants. Reverse osmosis, the most restrictive form of membrane filtration, is capable of removing even dissolved salts and ions.
In the pharmaceutical industry, membrane filters are integral to processes like sterile filtration, where they ensure the removal of microorganisms and particles from liquids, gases, and air. This is crucial in preventing contamination of pharmaceutical products during production, ensuring the safety and efficacy of drugs and medical solutions. Membrane filtration is also employed in biopharmaceutical manufacturing, aiding in the concentration and purification of proteins, enzymes, and other biomolecules.
The food and beverage industry also heavily relies on membrane filters to maintain product quality and safety. For instance, in dairy processing, microfiltration is used to extend the shelf life of milk by removing bacteria while preserving essential nutrients. Additionally, the wine industry employs membrane filtration for the clarification and stabilization of wines without altering their flavor profiles. Similarly, in the production of fruit juices, membrane filters help retain the natural flavors and colors while removing unwanted solids.
Membrane filters contribute significantly to environmental protection as well. In air quality control, they assist in removing particulate matter, allergens, and pollutants from industrial emissions, contributing to cleaner air and reduced health risks. Moreover, membrane filtration technologies are applied in wastewater treatment, enabling the removal of organic compounds, nutrients, and contaminants before discharge into natural water bodies. This plays a vital role in safeguarding aquatic ecosystems and maintaining water quality for human consumption.
In industrial biotechnology, membrane filters are employed in the downstream processing of bio-based products. They aid in the separation and concentration of biomass, enzymes, and biofuels, enhancing the efficiency of bioconversion processes. The use of membrane filters in this context helps reduce the energy and resource requirements for separation steps, making bioprocessing more sustainable and economically viable.
Despite their numerous benefits, the application of membrane filters also presents certain challenges. Fouling, a process where particles accumulate on the membrane surface, can lead to reduced filtration efficiency and increased maintenance requirements. Strategies to mitigate fouling include membrane surface modifications, regular cleaning, and optimized operating conditions. Membrane integrity is another concern, especially in industries where a compromised membrane could lead to product contamination. Rigorous quality control measures and regular integrity testing are essential to ensure consistent performance.
In conclusion, membrane filters serve as indispensable tools in various industrial processes by enabling selective separation, purification, and concentration of substances. From water treatment and pharmaceuticals to food and beverage production, these filters offer efficient and environmentally friendly solutions to complex separation challenges. Their ability to achieve separation based on size, charge, or other molecular properties makes them versatile and adaptable to diverse applications. As industries continue to advance, membrane filtration technologies will likely evolve and innovate, contributing to enhanced product quality, environmental sustainability, and economic efficiency.